Iso 2768 Hole Tolerance
Calculation of fits according ISO 286 (2010) The dimensions of a fit are calculated using the tolerances according to ISO 286 (2010). In addition to the deviations of shaft and hub, the span, clearance or interference of the fit is shown as result. The tolerances according ISO 286 are defined up to 3150mm or up to 500mm dependend on the selected tolerance field. These online calculations are provided free of charge.
The software is tested and no errors are known, but there is no warranty for the correctness of the results and for the availability of the calculations. The usage is at own risk. Nominal size D mm Tolerance hub.
Tolerances and fits This book includes tables and calculations for easy option of fits of machine parts and determination of their dimensional tolerances and deviations. Using this tool the following tasks can be solved:. Selection of suitable fits of machine parts according to the international standard ISO 286. Determination of dimensional tolerances and deviations of machine parts according to the international standard ISO 286.
Selection of preferred fits of machine parts and determination of their dimensional tolerances and deviations according to ANSI B4.1. Determination of non-prescribed limit deviations of linear and angular dimensions according to ISO 2768. Automatic design of a fit for the given clearance or fit interference respectively. The data, procedures, algorithms and specialized literature and standards ANSI, ISO, DIN and others were used in the calculations. List of standards: ANSI B4.1, ANSI B4.2, ISO 286, ISO 1829, ISO 2768, EN 20286, JIS B 0401. Information on the syntax and control of the calculation can be found in the document '.
It is necessary that the dimensions, shape and mutual position of surfaces of individual parts of mechanical engineering products are kept within a certain accuracy to achieve their correct and reliable functioning. Routine production processes do not allow maintenance (or measurement) of the given geometrical properties with absolute accuracy. Actual surfaces of the produced parts therefore differ from ideal surfaces prescribed in drawings. Deviations of actual surfaces are divided into four groups to enable assessment, prescription and checking of the permitted inaccuracy during production:. Dimensional deviations.
Shape deviations. Position deviations. Surface roughness deviations This toll includes the first group and can therefore be used to determine dimensional tolerances and deviations of machine parts. As mentioned above, it is principally impossible to produce machine parts with absolute dimensional accuracy. In fact, it is not necessary or useful. It is quite sufficient that the actual dimension of the part is found between two limit dimensions and a permissible deviation is kept with production to ensure correct functioning of engineering products. The required level of accuracy of production of the given part is then given by the dimensional tolerance which is prescribed in the drawing.
The production accuracy is prescribed with regards to the functionality of the product and to the economy of production as well. A coupling of two parts creates a fit whose functional character is determined by differences of their dimensions before their coupling. Basic size Dmax, Dmin. Limits of size for the hole dmax, dmin. Limits of size for the shaft ES.
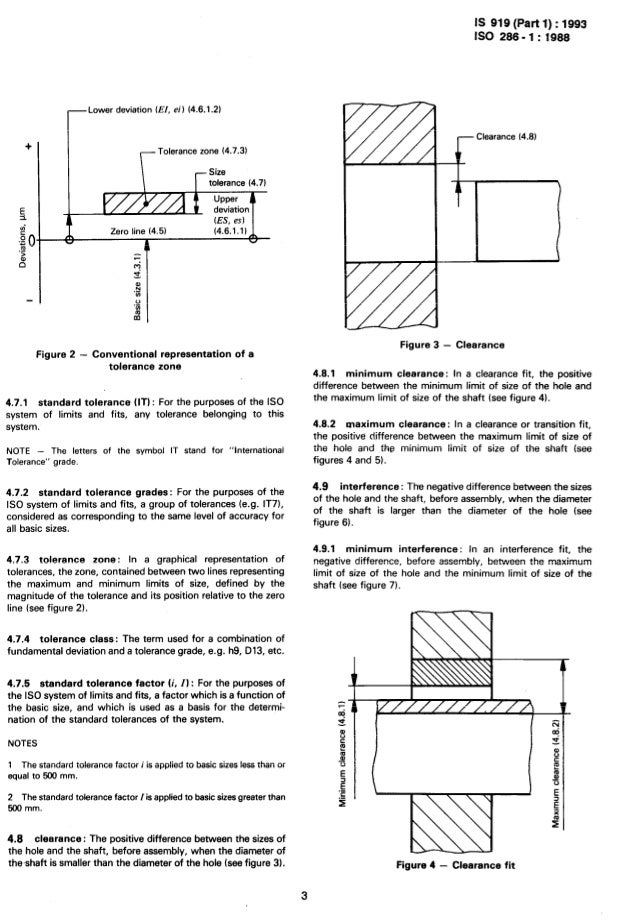
Hole upper deviation EI. Hole lower deviation es. Shaft upper deviation ei. Shaft lower deviation Depending on the mutual position of tolerance zones of the coupled parts, 3 types of fit can be distinguished:. Clearance fit. Transition fit.
Interference fit 1 This paragraph can be used to choose a fit and determine tolerances and deviations of machine parts according to the standard ISO 286:1988. This standard is identical with the European standard EN and defines an internationally recognized system of tolerances, deviations and fits.
The standard ISO 286 is used as an international standard for linear dimension tolerances and has been accepted in most industrially developed countries in identical or modified wording as a national standard (JIS B 0401, DIN ISO 286, BS EN 20286, CSN EN 20286, etc.). The system of tolerances and fits ISO can be applied in tolerances and deviations of smooth parts and for fits created by their coupling. It is used particularly for cylindrical parts with round sections. Tolerances and deviations in this standard can also be applied in smooth parts of other sections.
Similarly, the system can be used for coupling (fits) of cylindrical parts and for fits with parts having two parallel surfaces (e.g. Fits of keys in grooves). The term 'shaft', used in this standard has a wide meaning and serves for specification of all outer elements of the part, including those elements which do not have cylindrical shapes.
Also, the term 'hole' can be used for specification of all inner elements regardless of their shape. Note: All numerical values of tolerances and deviations mentioned in this paragraph are given in the metric system and relate to parts with dimensions specified at 20 °C. 1.1 Basic size. It is the size whose limit dimensions are specified using the upper and lower deviations.
In case of a fit, the basic size of both connected elements must be the same. Attention: The standard ISO 286 defines the system of tolerances, deviations and fits only for basic sizes up to 3150 mm. 1.2 Tolerance of a basic size for specific tolerance grade. The tolerance of a size is defined as the difference between the upper and lower limit dimensions of the part. In order to meet the requirements of various production branches for accuracy of the product, the system ISO implements 20 grades of accuracy.
Each of the tolerances of this system is marked 'IT' with attached grade of accuracy (IT01, IT0, IT1. Field of use of individual tolerances of the system ISO: IT01 to IT6 For production of gauges and measuring instruments IT5 to IT12 For fits in precision and general engineering IT11 to IT16 For production of semi-products IT16 to IT18 For structures IT11 to IT18 For specification of limit deviations of non-tolerated dimensions Note: When choosing a suitable dimension it is necessary to also take into account the used method of machining of the part in the production process. The dependency between the tolerance and modification of the surface can be found in the table in paragraph 5. 1.3 Hole tolerance zones. The tolerance zone is defined as a spherical zone limited by the upper and lower limit dimensions of the part. The tolerance zone is therefore determined by the amount of the tolerance and its position related to the basic size.
The position of the tolerance zone, related to the basic size (zero line), is determined in the ISO system by a so-called basic deviation. The system ISO defines 28 classes of basic deviations for holes. These classes are marked by capital letters (A, B, C. Autocad 2006 crack free download.
The tolerance zone for the specified dimensions is prescribed in the drawing by a tolerance mark, which consists of a letter marking of the basic deviation and a numerical marking of the tolerance grade (e.g. H7, H8, D5, etc.). This paragraph includes graphic illustrations of all tolerance zones of a hole which are applicable for the specified basic size 1.1 and the tolerance grade IT chosen from the pop-up list. Though the general sets of basic deviations (A. ZC) and tolerance grades (IT1.
Iso 2768 Mk Standard Tolerance
IT18) can be used for prescriptions of hole tolerance zones by their mutual combinations, in practice only a limited range of tolerance zones is used. An overview of tolerance zones for general use can be found in the following table.
Iso 2768 Mk Diameter Tolerance
The tolerance zones not included in this table are considered special zones and their use is recommended only in technically well-grounded cases.